I just saw this earlier and had to try it out.
Stronger than cast aluminum, a little lighter and tougher than cast iron, and you can make it on a hot plate.
Link.
Basically, melt 71 parts zinc, and dissolve into it 27 parts aluminum and 2 parts copper. The copper takes awhile so you'll want to have it in there from the start. I just poured some into a puddle then tested its machinability by drilling and threading it, which was quite easy. The threads are a little rough, but that might just be my crappy harbor freight taps.
Finally I put it in a vise and broke it into pieces with a hammer and pliers. It's a little bit brittle, but still takes a good smack to break apart. I might play with the alloy ratios to see if it can be made softer.
This might be good for casting some hard-to-find small fittings.
So, while I go turn on all the fans in the house and drink a half gallon of milk, any thoughts on this? Seems like it could open up some options to those without an extensive machine shop.
Neat little stovetop alloy
- mobile chernobyl
- Corporal 3
- Posts: 756
- Joined: Sun Dec 03, 2006 11:53 am
- Been thanked: 7 times
Most likely... I bought a little $20 set from there thinking it would be good for a single use tap in stainless... not even close - nearly F'd up my whole part! When it comes to tools like that, HF is not my first choice lol.Fnord wrote:The threads are a little rough, but that might just be my crappy harbor freight taps.
Nice Scooby key btw.
- Brian the brain
- Moderator
- Posts: 3497
- Joined: Mon Dec 05, 2005 2:06 am
- Location: Holland
- Been thanked: 7 times
Wait,..this only works with an electric stove right?
I have been wanting to do some casting myself...breechblock and such.
With the lost wax method I could make decorated yet funtional stuff....wow!!
Would it be doable on a charcoal fire?
What is used to actually contain the metals as they melt?
I have been wanting to do some casting myself...breechblock and such.
With the lost wax method I could make decorated yet funtional stuff....wow!!
Would it be doable on a charcoal fire?
What is used to actually contain the metals as they melt?
Gun Freak wrote:
Oh my friggin god stop being so awesome, that thing is pure kick ass. Most innovative and creative pneumatic that the files have ever come by!
Can't ask for a better compliment!!
Oh my friggin god stop being so awesome, that thing is pure kick ass. Most innovative and creative pneumatic that the files have ever come by!
Can't ask for a better compliment!!
- Fnord
- First Sergeant 2
- Posts: 2239
- Joined: Tue Feb 13, 2007 9:20 pm
- Location: Pripyat
- Been thanked: 1 time
- Contact:
You can use any heat source that gets over 800F or so. With a charcoal fire you could even melt and alloy brass, but if you're casting a lot you may want to pump some air to it with a fan or hair dryer.
For a container (crucible), any old steel container will do, but it would be better if it was a bit thicker than say, a soup can. A 2" steel end cap with a nip threaded into it will do fine. File a little spout into it so you'll have an easier time pouring.
BTB, it may also interest you to know this alloy seems to be good for casting because it really works its way into the mold well. Plain aluminum tends to ignore corners and fine details.
For a container (crucible), any old steel container will do, but it would be better if it was a bit thicker than say, a soup can. A 2" steel end cap with a nip threaded into it will do fine. File a little spout into it so you'll have an easier time pouring.
BTB, it may also interest you to know this alloy seems to be good for casting because it really works its way into the mold well. Plain aluminum tends to ignore corners and fine details.
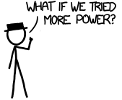
- Brian the brain
- Moderator
- Posts: 3497
- Joined: Mon Dec 05, 2005 2:06 am
- Location: Holland
- Been thanked: 7 times
These parts...are they by weight or size?Basically, melt 71 parts zinc, and dissolve into it 27 parts aluminum and 2 parts copper.
Gun Freak wrote:
Oh my friggin god stop being so awesome, that thing is pure kick ass. Most innovative and creative pneumatic that the files have ever come by!
Can't ask for a better compliment!!
Oh my friggin god stop being so awesome, that thing is pure kick ass. Most innovative and creative pneumatic that the files have ever come by!
Can't ask for a better compliment!!
- POLAND_SPUD
- Captain
- Posts: 5402
- Joined: Sat Oct 13, 2007 4:43 pm
- Been thanked: 1 time
sure but I'd feel safer with something more malleable and less brittleBTB, it may also interest you to know this alloy seems to be good for casting because it really works its way into the mold well. Plain aluminum tends to ignore corners and fine details.
Children are the future
unless we stop them now
unless we stop them now
-
- Staff Sergeant 3
- Posts: 1769
- Joined: Mon Mar 21, 2011 5:41 pm
So Fnord, does this mean that all of those pennies I have laying around wasting away, I could reuse to make custom parts? And how would I make a form for a block that would be used with a pneumatic cylinder and QEV combo?
It basically what was known as "pot metal" years ago.
"The primary component of pot metal is zinc, but often the caster adds other metals to the mix to strengthen the cast part, improve the flow of the molten metal, or to reduce cost.[dubious – discuss] With a low melting point of 419 °C (786 °F), zinc is often alloyed with other metals including lead, tin, aluminium and copper."
See link:
http://en.wikipedia.org/wiki/Pot_metal
"The primary component of pot metal is zinc, but often the caster adds other metals to the mix to strengthen the cast part, improve the flow of the molten metal, or to reduce cost.[dubious – discuss] With a low melting point of 419 °C (786 °F), zinc is often alloyed with other metals including lead, tin, aluminium and copper."
See link:
http://en.wikipedia.org/wiki/Pot_metal
- jimmy101
- Sergeant Major 2
- Posts: 3206
- Joined: Wed Mar 28, 2007 9:48 am
- Location: Greenwood, Indiana
- Has thanked: 6 times
- Been thanked: 18 times
- Contact:
A modern US penny is 97.5% Zn and 2.5% Cu (80 parts Zn to 2 part Cu), which would be a reasonable starting point. Need to add Al and a little Cu.71 parts zinc, and dissolve into it 27 parts aluminum and 2 parts copper"

-
- Private
- Posts: 18
- Joined: Wed Aug 29, 2012 5:24 pm
- Location: suffolk,variation
finally i find a thread that i can talk with some authority. ive been working in a foundry for over a year and doing metal casting as a hobby for over 5 years. the reason that alloy is so brittle is because of the zinc it makes alloys harder yet much more brittle. a good way to get your feet wet with this kind of thing is to start off with a charcoal fire with a little bit of forced air. most beginners use a steel crucible. DO NOT use a bean can they will burn through very quick and at the worst of times. the best bet is to use a stainless steel cup of some sort and line it with clay on the inside( so as not to absorb the iron from the steel.) i find that a decent alloy with alright strength and machine-ability is a brass that some call high brass its 65% copper and 35% zinc by weight personally i would add a small maybe .5% of aluminum to help with corrosion resistance. if any one wants to know more about metal casting don't hesitate to give me a holler .
Go big or go home.
If its worth doing its worth over doing
If its worth doing its worth over doing