Semi-auto Vortex Cannon! (SUCCESS)
- POLAND_SPUD
- Captain
- Posts: 5402
- Joined: Sat Oct 13, 2007 4:43 pm
- Been thanked: 1 time
Interesting findings. Now it would be a good idea to try higher pressures (though your findings suggest that you might have to find a way to further limit chamber size)
Children are the future
unless we stop them now
unless we stop them now
- shiddymunkie
- Private 2
- Posts: 33
- Joined: Mon Mar 03, 2014 9:27 pm
So the plug I'm using looks like this:POLAND_SPUD wrote:Interesting findings. Now it would be a good idea to try higher pressures (though your findings suggest that you might have to find a way to further limit chamber size)
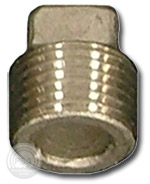
And here's a pic of it in the QEV:
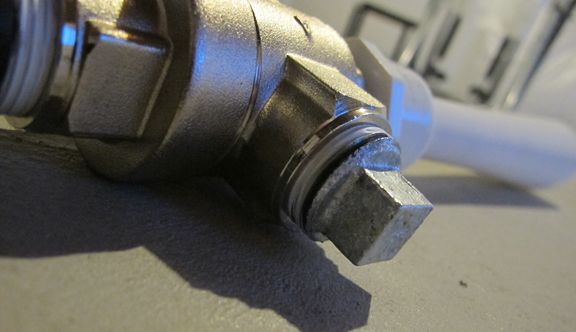
When fully tightened, the plug doesn't add any capacity to the QEV because the squared section is solid metal. However, the threaded area of the plug is hollow, which means I could reduce the capacity a little by filling up that hollow space with epoxy. I'm not sure how much of a difference it would make (or what the PSI limit is for the 0-link chamber as it is now) but seeing the difference between the 0-link and 1-link chamber, I expect it'd be noticeable if the right PSI can be achieved.
But here's the dilemma. The weakest part of this rig is the QEV which is rated to 150 PSI. The next weakest component is the pump, which caps out at 160 PSI. I could probably get the cannon up to 160 PSI as it stands now, but I wouldn't want to do that too many times and cause damage to the valves and pump...maybe just enough to see if the 0-link chamber reliably produces vortexes at the pressure. But in the end, if I am looking to increase PSI much beyond 150, I'm going to have to change multiple things in the design. I'm having trouble finding a 3/4 QEV rated for much higher than the 150 PSI mark, plus I'd need to find a new way to compress the air to that pressure anyway, and both of those things equal $$$.
Don't get me wrong, random projects like this are a hobby of mine and so I am fine spending some of my personal cash to get the results I want (as I'm able, of course). But if I'm giving myself the go-ahead to do that, I want to know what my options are. Is there a way to bypass needing a QEV but still get fast/high volume air flow? How about bypassing the slide valve and still retain the semi-auto functionality? This is why I kept going back to the idea of modding a cheap paintball marker...it appears to have all of the working part's I would need, but I wouldn't want to buy a marker only to find that something about it's design is not going to work for my needs.
- POLAND_SPUD
- Captain
- Posts: 5402
- Joined: Sat Oct 13, 2007 4:43 pm
- Been thanked: 1 time
You can push that QEV a little bit you know. I used a 3/4" one at 500 psi. I am sure someone here tried going higher than that. 200 or 250 psi would be fine
Now if you have to limit the chamber size you might consider limiting the volume of the QEV. Of course only if you experience problems at higher pressures
Now if you have to limit the chamber size you might consider limiting the volume of the QEV. Of course only if you experience problems at higher pressures
Children are the future
unless we stop them now
unless we stop them now
- shiddymunkie
- Private 2
- Posts: 33
- Joined: Mon Mar 03, 2014 9:27 pm
Oh wow, ok. I figured the 150 PSI rating had some sort of buffer built into it but I didn't think it'd be that high. That's good to know!POLAND_SPUD wrote:You can push that QEV a little bit you know. I used a 3/4" one at 500 psi. I am sure someone here tried going higher than that. 200 or 250 psi would be fine
The other thing I noticed was that the power of the vortexes could vary noticeably from shot to shot (sometimes as much as 1.5" on the pendulum) despite having the same chamber size and PSI. I attributed this to the speed at which I was pulling the slide valve back. In every test I tried to do this as quickly as possible without compromising accuracy, but I guess there was some variation. I eventually did so many tests on each chamber and pressure that I got a good idea of what to expect of a "good" pull. The point of that little story was seeing just how much of a difference there is between a sort-of-fast pilot and a really-fast pilot. Aside from keeping it greased up, are there any suggestion on how I can optimize the pilot time? I have a modded sprinkler valve + blowgun laying around if that helps...
- POLAND_SPUD
- Captain
- Posts: 5402
- Joined: Sat Oct 13, 2007 4:43 pm
- Been thanked: 1 time
This has always been a problem with manually actuated pilot valves. It can only be fixed by
1.Switching to a better pilot valve or cascaded design (extra QEV to help in piloting). Though that still doesn't fix anything - it's 'get a bigger hammer' approach
2.Solenoid valves. This method has it's own limitations - mainly flow and pressure rating, but it does make piloting consistent
1.Switching to a better pilot valve or cascaded design (extra QEV to help in piloting). Though that still doesn't fix anything - it's 'get a bigger hammer' approach
2.Solenoid valves. This method has it's own limitations - mainly flow and pressure rating, but it does make piloting consistent
Children are the future
unless we stop them now
unless we stop them now
- matti
- Specialist 2
- Posts: 252
- Joined: Tue Oct 04, 2005 1:01 pm
- Has thanked: 1 time
- Been thanked: 1 time
It seems that you can make part drawings and order 3D printed parts, so I would suggest that you design and have 3D printed a pistol grip with some kind of springs to pull open the slide valve.. that would give you fast and consistent pilotingshiddymunkie wrote:Aside from keeping it greased up, are there any suggestion on how I can optimize the pilot time? I have a modded sprinkler valve + blowgun laying around if that helps...
to clarify little more, I mean that you connect the pistol grip to gun and some springs to slide valve sliding part and then you somehow cock the spring system and have a trigger to release the springs/slide valve. (you can look at some crossbow trigger systems to get some ideas on how to construct a release trigger assembly).
Of course you can also do it without 3D printing and with some basic tools

- shiddymunkie
- Private 2
- Posts: 33
- Joined: Mon Mar 03, 2014 9:27 pm
Just checked 160 PSI and 150 PSI with the 0-link chamber, no dice. I hope filling that plug with epoxy will get me close to 160 PSI. If it can't, I suppose I can open the QEV up and take a look at other ways I can reduce volume...but honestly, it seems like I'm getting close to the limit of my current design, and I'm wondering if my time would be better used in finding a design that avoids some of the inherent shortfalls of this one.POLAND_SPUD wrote: Now if you have to limit the chamber size you might consider limiting the volume of the QEV. Of course only if you experience problems at higher pressures
On a side note, I think I figured out a cheap-n-easy DIY way to make cones if anyone wants to experiment; poster board reinforced with layers of duct tape. Basically the poster board (or any heavy gauge paper) would be used to create the cone shape. It's inexpensive and very easy to work with -- all you would need is some basic math skills, scissors, and some means to draw circles (string or large protractor). Once your paper cone has all the right specs, you'd then wrap it in several layers of duct tape. Given the cone's shape, and the fact that the brunt of the force is going to be on the PVC coupling you'd use as the throat, this approach should be sufficient in terms of strength. I was actually thinking of making an extension for my cone using this method to see if it would enable me to use larger chambers.
Where would a secondary QEV go in my setup to accomplish the cascading effect? I have a modded sprinkler valve just collecting dust, I might as well put it to use if it can help.POLAND_SPUD wrote:This has always been a problem with manually actuated pilot valves. It can only be fixed by
1.Switching to a better pilot valve or cascaded design (extra QEV to help in piloting). Though that still doesn't fix anything - it's 'get a bigger hammer' approach
I see what you're saying, but 3D printing isn't cheap (and time/labor = money too). I'd invest the money (or time) if I knew such a mechanism would offer significant improvements in performance, but I think I'm already at about 90% of what the rig is capable of. Unless I could repurpose a trigger from something else, or make a very simple one from scratch with minimal time/labor, I'm not sure if it'd be worth it.matti wrote:It seems that you can make part drawings and order 3D printed parts, so I would suggest that you design and have 3D printed a pistol grip with some kind of springs to pull open the slide valve.. that would give you fast and consistent pilotingshiddymunkie wrote:Aside from keeping it greased up, are there any suggestion on how I can optimize the pilot time? I have a modded sprinkler valve + blowgun laying around if that helps...
to clarify little more, I mean that you connect the pistol grip to gun and some springs to slide valve sliding part and then you somehow cock the spring system and have a trigger to release the springs/slide valve. (you can look at some crossbow trigger systems to get some ideas on how to construct a release trigger assembly).
Of course you can also do it without 3D printing and with some basic tools
What about HPA tank > hammer valve > cone? Would something like that work (a tiny burst of 500 - 800 PSI air)?
- matti
- Specialist 2
- Posts: 252
- Joined: Tue Oct 04, 2005 1:01 pm
- Has thanked: 1 time
- Been thanked: 1 time
When you are limiting the volume of valve/chamber don't forget that there is a dead space between cone throat and valve opening. Pressure at the cone throat is important and it's what makes the difference in vortex power and speed.. Now if you limit the volume of your chamber and use higher pressure the dead space will lower the high pressure low volume air back to lower pressure before the throat of the cone.
You need longer/bigger cone or smaller throat to use this at high pressures.
You need longer/bigger cone or smaller throat to use this at high pressures.
- shiddymunkie
- Private 2
- Posts: 33
- Joined: Mon Mar 03, 2014 9:27 pm
See, I never would have thought that making the throat smaller than it already is would increase performance, I would have assumed the opposite. I think it's worth a try. With that being said, one of my concerns with your advice has to do with initiating the vortex. The reason there is dead space in the chamber is to allow the air flow to expand a bit just before reaching the smaller throat of the cone. This abrupt flow restriction from big to small is what appears to start the toroidal motion:matti wrote:When you are limiting the volume of valve/chamber don't forget that there is a dead space between cone throat and valve opening. Pressure at the cone throat is important and it's what makes the difference in vortex power and speed.. Now if you limit the volume of your chamber and use higher pressure the dead space will lower the high pressure low volume air back to lower pressure before the throat of the cone.
You need longer/bigger cone or smaller throat to use this at high pressures.

If I fill the dead air in the chamber, there will be a less of an abrupt flow restriction. Instead of the air going from 1" to 1/2" , it would only go from 3/4" to 1/2". Some degree of "pinch" appears to be necessary start the vortex in motion, but I am not sure if going from 3/4" to 1/2" is enough of one...

- shiddymunkie
- Private 2
- Posts: 33
- Joined: Mon Mar 03, 2014 9:27 pm
Well, some good and bad news.
I picked up an airzooka for comparison sake, and quite frankly, it's owning my cannon. Don't get me wrong -- my cannon has a much better power-to-air volume ratio, but the superior efficiency just can't overcome the sheer air volume the airzooka is pushing (several hundred times what my cannon is putting out). I have no doubts that I could easily best the airzooka with a bigger cone, because a bigger cone would allow for a bigger chamber. In fact, I'd wager than I could produce a more powerful vortex cannon with a chamber 1/10 the size of the airzooka, but that's neither here nor there. The objective of the project was to create a vortex cannon that was:
1. Smaller than an Airzooka
This is only possible with a small cone, but small cone = weak vortexes due to the air volume/PSI constraints.
2. More powerful than an Airzooka
Aside from using combustion (i.e. vortex ring gun), this only seems possible with a much larger cone and chamber. None of those options seems compatible with my intended use for this cannon.
3. Office friendly
This is where my cannon was doomed from the start. It's loud as all hell and sort of looks like DIY blunderbust/pipe-bomb. And that's just as it stands now. Add a 3-foot cone, huge chamber, and what I can only imagine would be a thunderous boom upon valve release...I'm going to have problems if I bring that into work and start shooting it at people. That's not to mention the logistical problems of having a compressed air supply on site.
As such, the project is being discontinued until further notice as the Airzooka beats my cannon in all three of the above criteria. This is the bad news. The good news is that an affordable, accessible, and sufficiently-powerful-for-my-needs vortex cannon already exists for anyone who also wants one -- and it's called an Airzooka. No, it's not nearly as cool as making your own, but if you're looking for results, its the way to go unless you're willing to go big (literally).
:blackeye:
I picked up an airzooka for comparison sake, and quite frankly, it's owning my cannon. Don't get me wrong -- my cannon has a much better power-to-air volume ratio, but the superior efficiency just can't overcome the sheer air volume the airzooka is pushing (several hundred times what my cannon is putting out). I have no doubts that I could easily best the airzooka with a bigger cone, because a bigger cone would allow for a bigger chamber. In fact, I'd wager than I could produce a more powerful vortex cannon with a chamber 1/10 the size of the airzooka, but that's neither here nor there. The objective of the project was to create a vortex cannon that was:
1. Smaller than an Airzooka
This is only possible with a small cone, but small cone = weak vortexes due to the air volume/PSI constraints.
2. More powerful than an Airzooka
Aside from using combustion (i.e. vortex ring gun), this only seems possible with a much larger cone and chamber. None of those options seems compatible with my intended use for this cannon.
3. Office friendly
This is where my cannon was doomed from the start. It's loud as all hell and sort of looks like DIY blunderbust/pipe-bomb. And that's just as it stands now. Add a 3-foot cone, huge chamber, and what I can only imagine would be a thunderous boom upon valve release...I'm going to have problems if I bring that into work and start shooting it at people. That's not to mention the logistical problems of having a compressed air supply on site.
As such, the project is being discontinued until further notice as the Airzooka beats my cannon in all three of the above criteria. This is the bad news. The good news is that an affordable, accessible, and sufficiently-powerful-for-my-needs vortex cannon already exists for anyone who also wants one -- and it's called an Airzooka. No, it's not nearly as cool as making your own, but if you're looking for results, its the way to go unless you're willing to go big (literally).
:blackeye:
- Anatine Duo
- Specialist
- Posts: 189
- Joined: Sat Feb 01, 2014 11:16 am
- Location: cottage country
- Has thanked: 40 times
- Been thanked: 20 times
Well, I learned a lot from your project, and at least you have the valve and variable volume chamber for more experiments!
- shiddymunkie
- Private 2
- Posts: 33
- Joined: Mon Mar 03, 2014 9:27 pm
Indeed, and I wouldn't be surprised if I end up revisiting this vortex cannon at some point in the future. If I do, it probably won't be as an office toy because that one constraint really tied my hands with this project. But without size, noise, and air supply being an issue, I'm sure I could make one that was "scary" powerful, now that I have a better understanding of how these things function.
- Gregarious Oddfellow
- Recruit
- Posts: 2
- Joined: Fri Apr 18, 2014 3:04 pm
I'm working on a pneumatic vortex ring generator too - of a larger scale, like shiddymunkie wants for his next 
Unfortunately, I’ve found limited information on how vortex rings actually form.
Ring variables that I can think of:
1. stability / longevity before it dissipates
2. forward velocity
3. rotational velocity
4. inner diameter
5. outer diameter
Gun variables I think might set the above-listed variables:
1. gas pressure in chamber
2. gas/chamber volume
3. valve speed & size
4. barrel
5. nozzle diameter (the restriction-plate)
6. cone: angle/diameter-at-end
7. cone: length
I will do science to them.
But with this many independent variables, testing will take a really long time. And designing the gun to vary all these ways constrains construction options.
So if anyone has done any of the physics/math/engineering/testing, I’d love to use their results to reduce the number of variables I’m contending with. (I'm looking at you shiddymunkie, matti, anyone else who's built one, anyone who took more physics/engineering classes than me...)
I'm really hoping someone can point me towards some answers.
After lengthy Google-ing, all I've found online are sites like "build one this weekend with your kid from cardboard" - which are useless. Or sites with papers from "Journal of Fluids Engineering" or the like, which all start with 5 pages of formulas where I don't recognize half the symbols -- and am unsure if I remember enough calculus to solve them even if I had values for those symbols

Unfortunately, I’ve found limited information on how vortex rings actually form.
Ring variables that I can think of:
1. stability / longevity before it dissipates
2. forward velocity
3. rotational velocity
4. inner diameter
5. outer diameter
Gun variables I think might set the above-listed variables:
1. gas pressure in chamber
2. gas/chamber volume
3. valve speed & size
4. barrel
5. nozzle diameter (the restriction-plate)
6. cone: angle/diameter-at-end
7. cone: length
I will do science to them.
But with this many independent variables, testing will take a really long time. And designing the gun to vary all these ways constrains construction options.
So if anyone has done any of the physics/math/engineering/testing, I’d love to use their results to reduce the number of variables I’m contending with. (I'm looking at you shiddymunkie, matti, anyone else who's built one, anyone who took more physics/engineering classes than me...)
I'm really hoping someone can point me towards some answers.
After lengthy Google-ing, all I've found online are sites like "build one this weekend with your kid from cardboard" - which are useless. Or sites with papers from "Journal of Fluids Engineering" or the like, which all start with 5 pages of formulas where I don't recognize half the symbols -- and am unsure if I remember enough calculus to solve them even if I had values for those symbols

- Gregarious Oddfellow
- Recruit
- Posts: 2
- Joined: Fri Apr 18, 2014 3:04 pm
If I can't narrow down any of those variables via research, I'll attempt to build a vortex gun that can change as many of those as possible.
Here's my plan:
Gas pressure in chamber: set at air-compressor/compressed-gas-cylinder via gauge/regulator
Chamber volume: I plan to copy shiddymunkie’s design of PVC fittings that screw together.
Valve speed & size: I have a 1” sprinkler valve ( After reading thru the spud files forum, it sounds like that may not have been the best choice. I'm not too worried about this, as there are lots of commercial valves and I can just buy a bigger/faster one if my current valve doesn't work well.
Barrel: All the valve diagrams I've seen look like they disrupt gas flow a lot while opening. I hypothesize that a more laminar gas flow would make a more stable vortex. So I intend to test some flow-regulating options, trading gas-pressure at nozzle for more laminar flow.
Option A) No gap - valve exit touches the nozzle.
Option B) Barrel - valve opens into a barrel, with nozzle at the other end. How long should the barrel be? What diameter compared to my valve opening? I'm constructing a nested-PVC telescoping barrel to test length. I'll need multiple barrels to vary diameter.
Option C) Barrel full ‘o straws - try to encourage laminar flow with straws, something like this: http://www.instructables.com/id/Laminar ... /?ALLSTEPS. What straw diameter/length? What diameter barrel? How much gap between valve-opening and straws, between straws and nozzle?
Nozzle diameter: I’m going to build an iris valve for end of barrel. This approximates a circular opening of arbitrary size (more leaves = better approximation of circle). I’m having trouble finding information on the ratios for this too - I've found some patterns but not an explanation of how to change them for a different size iris with more leaves.
Cone: I can build a couple of these out of cheap plastic sheeting or cardboard.
matti - where’d you get the info that 20º-30º cone angle?
shiddymunkie - how’d you calculate you should have an 8.6º cone angle? How’d you pick the length?
----
After I have a working prototype:
Particulates in the vortex - glitter, chalk dust, aerosolized liquids, etc.
I’ve heard those get driven out of the vortex fairly quickly due to centrifugal forces and the additives being denser than the gas.
In which case, would a lower rotational velocity keep them in the vortex longer? Would that reduce ring stability? I guess I'll find out.
----
just for fun: largest man-made vortex ring generator I’ve found to date:
Here's my plan:
Gas pressure in chamber: set at air-compressor/compressed-gas-cylinder via gauge/regulator
Chamber volume: I plan to copy shiddymunkie’s design of PVC fittings that screw together.
Valve speed & size: I have a 1” sprinkler valve ( After reading thru the spud files forum, it sounds like that may not have been the best choice. I'm not too worried about this, as there are lots of commercial valves and I can just buy a bigger/faster one if my current valve doesn't work well.
Barrel: All the valve diagrams I've seen look like they disrupt gas flow a lot while opening. I hypothesize that a more laminar gas flow would make a more stable vortex. So I intend to test some flow-regulating options, trading gas-pressure at nozzle for more laminar flow.
Option A) No gap - valve exit touches the nozzle.
Option B) Barrel - valve opens into a barrel, with nozzle at the other end. How long should the barrel be? What diameter compared to my valve opening? I'm constructing a nested-PVC telescoping barrel to test length. I'll need multiple barrels to vary diameter.
Option C) Barrel full ‘o straws - try to encourage laminar flow with straws, something like this: http://www.instructables.com/id/Laminar ... /?ALLSTEPS. What straw diameter/length? What diameter barrel? How much gap between valve-opening and straws, between straws and nozzle?
Nozzle diameter: I’m going to build an iris valve for end of barrel. This approximates a circular opening of arbitrary size (more leaves = better approximation of circle). I’m having trouble finding information on the ratios for this too - I've found some patterns but not an explanation of how to change them for a different size iris with more leaves.
Cone: I can build a couple of these out of cheap plastic sheeting or cardboard.
matti - where’d you get the info that 20º-30º cone angle?
shiddymunkie - how’d you calculate you should have an 8.6º cone angle? How’d you pick the length?
----
After I have a working prototype:
Particulates in the vortex - glitter, chalk dust, aerosolized liquids, etc.
I’ve heard those get driven out of the vortex fairly quickly due to centrifugal forces and the additives being denser than the gas.
In which case, would a lower rotational velocity keep them in the vortex longer? Would that reduce ring stability? I guess I'll find out.
----
just for fun: largest man-made vortex ring generator I’ve found to date:
- matti
- Specialist 2
- Posts: 252
- Joined: Tue Oct 04, 2005 1:01 pm
- Has thanked: 1 time
- Been thanked: 1 time
I don't have much time right now, but few short answers here..
Cone angles I figured from my studies of SUTTON's Rocket Propulsion Elements book.I have the eighth edition, Sutton's book is a 800 page text and it's has been regarded as the best sourcebook on rocket propulsion.. A very good book to read !
On Sutton's book there is also very detailed information of mathematical formulas and how to use those for calculating different things for nozzles and chambers etc..
Other thing that you would probably like to read is the paper of Army Research Laboratorys vortex generator (is high pressure and we cant talk about it too much here because of the propellant it uses.) Don't take too much information from this paper, it's quite different thing to launch vortex with low pressure air. (LINK: http://www.dtic.mil/dtic/tr/fulltext/u2/a372518.pdf )
Don't wait for spectacular results and power from relatively low pressure pneumatic vortex launcher. With hybrid you can get some very nice results like I did.
Waiting to hear the results you will gather from this project. You can also PM me if you have some specific questions
Cone angles I figured from my studies of SUTTON's Rocket Propulsion Elements book.I have the eighth edition, Sutton's book is a 800 page text and it's has been regarded as the best sourcebook on rocket propulsion.. A very good book to read !
On Sutton's book there is also very detailed information of mathematical formulas and how to use those for calculating different things for nozzles and chambers etc..
Other thing that you would probably like to read is the paper of Army Research Laboratorys vortex generator (is high pressure and we cant talk about it too much here because of the propellant it uses.) Don't take too much information from this paper, it's quite different thing to launch vortex with low pressure air. (LINK: http://www.dtic.mil/dtic/tr/fulltext/u2/a372518.pdf )
Don't wait for spectacular results and power from relatively low pressure pneumatic vortex launcher. With hybrid you can get some very nice results like I did.
Waiting to hear the results you will gather from this project. You can also PM me if you have some specific questions
